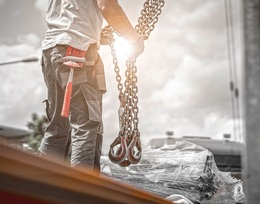
With a new administration in Washington focusing efforts on trying to bolster the economy, there is some uncertainty about what that could mean for the different industries counted upon to help drive that growth. One significant and consistent contributor to America’s economic well-being is the building and construction industry, which plays a substantial role in job growth and infrastructure improvement, accounting for approximately 4.5% of the nation’s GDP.
While it can be hard to accurately predict what lies ahead, there is some encouraging news coming from New Jersey, where forecasting appears sunny despite a cloudier outlook for the rest of the country.
The Associated Construction Contractors of New Jersey released a MarketCAST report for the fourth quarter of 2024 outlining how the state is bucking the national trend. Across the country, there was a 19% drop in construction starts, but the Garden State saw a 33% increase. What’s more, with a 6% increase in total construction spending in 2024, New Jersey is forecast to reach record high levels over the next few years, with the New Jersey Alliance for Action’s latest construction forecast predicting $29.7 billion being spent on construction in 2025 alone. And thanks to a slew of planned projects, including several earmarked in Gov. Phil Murphy’s FY2026 budget, there is certainly even more reason to be optimistic.
That’s not to say there aren’t several challenges still facing the industry. Recent headlines about tariffs on imported goods and materials have raised some eyebrows, while ongoing struggles like high interest rates, supply chain disruptions and a depleted labor force continue to have an impact. But the hope is that improving economic conditions as a whole will lead to increased demand for construction projects across various segments. This is forcing companies to stay ahead of the curve and prepare for the boom, getting creative along the way by upskilling their employees and embracing innovation to become more efficient.
With so many factors playing a role in both the short- and long-term future, South Jersey Biz gathered some leaders in the field to get a wide-ranging view on their industry, while also finding out how the lessons they’ve learned have better prepared them for what they can control as well as that which they cannot predict.
Looking at the current state of the industry, what are some of the bright spots and what are some of the biggest challenges that you are seeing?
“The local construction industry is booming and there is a lot of commercial and institutional construction projects being funded and developed. … The biggest challenges are lack of manpower and qualified contractors to perform the work, as well as uncertainty relative to future cost of equipment and materials. Contractors providing hard bids on long-term projects are at risk for unknown cost increases in the coming months as a tariff war is looming.”
—Chuck Romanoli, managing principal, NEW ROAD Construction Management
“I think the bright spot is that we keep moving forward. In regards to material—brick, stone and CMU (concrete masonry unit) are usually sourced within the United States, so we are not as affected [by potential trade wars]. Being in the U.S., we are not bringing our material over on a ship, so that reduces the cost and the carbon footprint. …So for us in the industry, we have steady movement going forward. People are making their employees come back to the office, which will rejuvenate [areas], and whenever there’s a rejuvenation, there’s the desire to build and create, and we are hoping to be part of that.”
—Amy Hennessey, executive director, Employing Bricklayers Association
With a lot of talk about supply chain disruptions and rising costs, are there any lessons learned from early in the pandemic that can be carried over to be better prepared for dealing with the issues?
“The pandemic caused a major disruption in the global supply chain. Lead times for certain building equipment and materials went from months to a year plus, with costs increasing substantially. The takeaway from this was to be more prepared for potential supply side issues and ready to act quickly to procure materials and equipment if disruptions to the market occur or have the potential to occur.”
—Robert Powell, CCIM, vice president of development and marketing, Vineland Construction Company
“The pandemic taught us that planning, adaptability and a strong, skilled workforce are essential to keeping the construction industry moving, even during the most uncertain times. … One of the most pressing issues we face is the need for deeper investment in Southern New Jersey. For too long, this region has been underserved—especially in manufacturing. I care immensely about South Jersey. As a board member of the Casino Reinvestment Development Authority, I’ve seen how public-private partnerships can unlock transformative growth. These investments have helped us weather the worst of the pandemic—and they must continue if we want to build a more resilient economy.”
—William Sproule, executive secretary-treasurer, Eastern Atlantic States Regional Council of Carpenters
“To protect our clients against supply chain disruptions and rising costs, architects, engineers and contractors need to stick to the basics of good project management. This means careful, insightful scheduling and pricing, based on the latest available data. We need to carefully develop conservative—as opposed to optimistic—pro forma that include contingencies and escalation, as well as accounting for all the ancillary project costs. ‘Other costs’ include permitting, environmental issues, security, furnishings, move-in and more, which, if not planned for, can explode a budget.”
—Regan Young, AIA, president, RYEBREAD Architects
“This is a time that designers and architects should really look at how things can be built and open up their minds. [They] pivoted in 2008 and 2009 and went to lumber; this is a time to maybe pivot again and start looking at brick, stone and CMU. … So many are trying to build cheaper and faster with other materials, and it’s not as safe. So I think it’s something where the commercial construction community really needs to take a look in the mirror because I think if we can ultimately pivot that branch of the industry, the better off we will be.”
—Amy Hennessey
How else are you able to stay ahead of the curve to mitigate the risks that can impact construction?
“Design professionals need to protect our clients’ interests in the face of evolving project delivery options: design/build, co-ops/consortiums, utility/improvement authority generated funding and management. While some of these alternatives offer convenience, clients still need professionals to look at long-term value, dependability and warranties to protect them after project completion.”
—Regan Young
“Proper planning and identifying critical items in the schedule are key. We proactively identify potential issues ahead of time and procure essential items well in advance to mitigate risks during construction. Our team also works closely with municipal engineers and utility companies to avoid lengthy plan revisions or long response times.”
—Robert Powell
With labor shortages still impacting the industry, how are you looking to fill the void?
“EAS Carpenters has always kept pace with industry needs, offering continuing education for journeymen, including expanding training in areas like renewable energy, heavy highway, concrete and pile driving. We’re not just filling jobs, we’re building careers. … We are also working to develop the next generation of carpenters. In addition to our four-year, earn-while-you-learn apprenticeship programs, we offer pre-apprenticeship opportunities and partner with high schools, community groups, veterans’ organizations and women-in-construction initiatives.”
—William Sproule
With such a focus on energy efficiency and technological advancements these days, how has that changed your approach?
“We make every effort to pursue financial relief for our clients including grants, energy rebates, state incentives, solar, etc. There are minimum construction codes addressing energy efficiency, including increased R-value for roofs, occupancy sensors for lighting, increased fresh air requirements for HVAC systems and, of course, solar power continues to be a consideration. … Building animation during design is becoming more commonplace and is a great tool for clients to visualize the space and make more informed decisions.”
—Chuck Romanoli
Click here to subscribe to the free digital editions of South Jersey Biz.
To read the digital edition of South Jersey Biz, click here.
Published (and copyrighted) in South Jersey Biz, Volume 15, Issue 4 (April 2025).
For more info on South Jersey Biz, click here.
To subscribe to South Jersey Biz, click here.
To advertise in South Jersey Biz, click here.