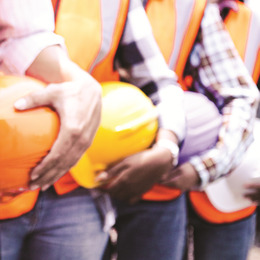
The business axiom of not fearing one’s competitors but rather learning from them might allude to the upper hand of providing stand-out service that differentiates exemplary services within a packed field, but representatives from the state’s manufacturing industry laud the merits of banding together to elevate their image together.
Whether it’s sharing information that yields better practices, directing others in the industry to cost-saving initiatives or working in tandem to support the organizations acting as the rising tide that raises all ships, teamwork is key to both advancing and advocating for an industry that’s still navigating erroneous perceptions impacting its overall image.
“People think manufacturing is low-skill, repetitive jobs,” says Rosa Crespo, HR head of the Marlton-based packaging company T.H.E.M. and a member of the Manufacturing Alliance of South Jersey.
She adds that manufacturing diligently keeps pace with modern trends and technological advancements, and has accordingly evolved with changes ushered in by the likes of cutting-edge robotics, AI and internet-connected smart devices. “Modern manufacturing requires a highly skilled workforce, integration of automation, robotic, data-driven systems. There’s a lot of employees who are needed with technical expertise that I don’t think people realize you need to work with advanced machinery.”
Steve Tice, also a member of the Manufacturing Alliance of South Jersey, is VP of operations for the West Deptford-based manufacturer of custom flexible items Lamatek, a role that he’s worked his way up to across the 27 years since joining the team as an entry-level employee—a testament, he explains, to on-the-job training available to the sector’s newcomers. He, too, has seen how the industry has grown, adapted and thrived in recent years, especially as many of its operators were actually advantageously positioned to meet the pandemic with a flexibility that created pathways to brand-new opportunities.
“Within a day of the pandemic, we were able to make some minor adjustments to our equipment and we were making all of the components to the face shields—that got us into a whole new industry we weren’t in,” he explains. “That opened doors into medical markets.”
In addition to regional entities like the Manufacturing Alliance of South Jersey, statewide industry professionals also have access to groups like the New Jersey Manufacturing Extension Program (NJMEP), which has come to serve a trade-association role in its advocacy, outreach and educational efforts.
NJMEP’s Director of Marketing & Communications Michael Womack notes that the organization has certainly run with those responsibilities, and support from beyond the industry has helped bolster its efforts to maintain positive momentum that also extends to an inclusivity and accessibility inviting hard-working folks of all backgrounds and at all stages of life to find their place in a field where “people can end their careers with a PhD.”
“The recent support that we’ve seen over the past five years in manufacturing, from the state specifically, has grown—it got scaled back a little bit in this fiscal year ’25 just due to the constraints of the economy but generally, it’s continued to increase and really helped put together grant-funded programs for those that were changing careers, veterans, veterans’ family members, those in disconnected rural or inner-city areas, and that has really helped NJMEP build out a robust workforce-develop program,” he affirms. “And this definition of ‘workforce development’ is truly building the workforce of tomorrow, not just supporting the current incumbent workers … All of the state support helps us fiscally ensure that our clients have a workforce for tomorrow.”
Crespo adds that recognizing talent from within also helps tap into that internal workforce’s vast potential while transferring their applied procedural knowledge to enriched leadership roles.
“We had a woman who was working in the line, and we realized that she just had a lot of potential,” she recalls. “She went from being a line lead, working and being the production supervisor for an area, and she’s now a production director. This is within a few years: She’s just taken off and now manages an entire building for us.”
Manufacturing aims to continue serving both its fellow organization comprising the local economic landscape and its residential neighbors alike. It wants to do so by greeting the future with forward-thinking priorities like increased efficiency and a smaller environmental footprint, which are also two concerns addressed by the New Jersey Economic Development Authority’s (NJEDA’s) statewide Manufacturing Voucher Program.
Developed in 2022 and now in its third round, the $20,000,000 pilot program aims to assist The Garden State’s manufacturers in their ability to both access and purchase the modern equipment enabling them to improve their efficiency, impact, productivity and profit by providing them with grants awards covering up to $250,000 in eligible equipment costs, helping them make the cutting-edge purchases that leads to better operations overall.
Tice’s company secured a voucher at round one; since then, he’s not only helped his fellow industry leaders navigate the application process but also testified before the state senate’s bipartisan manufacturing caucus “to get this grant renewed for year two and now subsequently year three.” And while he notes that “bringing in equipment is like a year-long process,” Tice adds that the payoff has been immediate for Lamatek: eliminating a step between manufacturer and customer, a more streamlined supply chain and “making a whole new list of customers happy.”
With T.H.E.M. being a round-two voucher awardee, Crespo and her team are just beginning that long process. But they already know how they want to allocate the award for companywide improvements—even beyond “unheard-of packing efficiencies in the high 90s” at one of its copacking facilities: upscaling machinery for increased production capabilities, enhanced quality and continuing “to meet the industry demands while we stay at the forefront.”
Making improvements today also means recognizing that decades of experience, wisdom and operational know-how are at risk of leaving the field as veterans of industry retire. Tice notes that while the longtimers with this institutional knowledge “have no problem with passing that along,” the looming exodus of an aging workforce does threaten to leave a void of talent and experience in its wake.
That’s one reason why student-outreach programs are widely championed by leaders in the manufacturing space as effective measures for encouraging young talent to discover their place in the field, whether it’s through internships, partnerships with area colleges, or bringing interactive education directly to middle and high school students.
“A past governor once said that all manufacturing is gone in New Jersey, and that has never been true … I have no doubt there will be growth in the industry, ” Womack says. He points to the success of NJMEP’s Future Makers & Creators Tour, a mobilized student-engagement program that has allowed more than 4,950 students across 12 counties so far in hands-on demonstrations of robotics, 3D printing, welding and more to spark their interest in a manufacturing career. “They know what kind of internships are available, they meet local people who work in manufacturing so they know who they can talk to, they know how to keep that conversation going while we’re also bringing awareness to the small and mid-size manufacturers who make up about 85% of the industry.”
“We like partnering with the local colleges,” Tice adds. “They’ll do simple courses like CPT, or certified production technician, for instance. It’s a four-week course that teaches them basic soft skills, safety, there’s some OSHA 10 in there … They get an understanding of what it’s like to work in a manufacturing environment so they’re not just graduating from high school and walking onto a manufacturing floor.”
As the industry’s professionals do their part to proactively position it for the most promising future possible, Crespo says that its strong inclination toward community is certainly one reason why she’s greeting the future as “an eternal optimist.”
“There’s a lot of different professional avenues [workers] can take in manufacturing that I think would definitely be advantageous to all of us: No day is the same, every day brings new challenges and we’re all there working as a team trying to tackle them,” she observes. “Whatever the future brings, we’re going to figure out how to work around it and with it.”
Click here to subscribe to the free digital editions of South Jersey Biz.
To read the digital edition of South Jersey Biz, click here.
Published (and copyrighted) in South Jersey Biz, Volume 15, Issue 4 (April 2025).
For more info on South Jersey Biz, click here.
To subscribe to South Jersey Biz, click here.
To advertise in South Jersey Biz, click here.